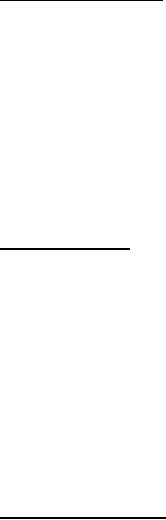
JOTP-011
5 December 2014
APPENDIX E. BREAKDOWN TEST AND CRITICAL ANALYSIS (BTCA)
E.2.7.5 Mechanical Properties.
Mechanical properties (such as tensile/compressive/ shear strength and hardness) of explosive
materials must be assessed at the full range of working temperatures for the munition. It will also
be necessary to test structural materials at temperature extremes for safety critical items, such as
rocket motor cases, in order to verify design safety margins. Typical methods will include uniaxial
tensile testing to STANAG 4506, Dynamic Mechanical Thermal Analysis (DMTA) to
STANAG 4540 and burst overpressure tests on rocket motor cases (although it may prove difficult
to conduct these as part of BTCA). It may also be necessary to assess fatigue crack growth for
some structural materials. The types of testing will ultimately be determined by the type of
material being tested.
E.2.7.6 Hazard Properties.
a. Repetition of the small scale tests to assess hazard properties must be undertaken. These
may include, but are not limited to, methods to determine ease of initiation by impact, friction and
electrical spark, along with temperature of ignition. Explosive material testing and assessment
should be conducted in accordance with STANAG 4170 and AOP-7.
b. Normally the small scale tests will be sufficient but larger scale tests may also be
required if an issue is identified. The exact methods used would depend upon the type and quantity
of material available for the tests but may include `gap tests' and tests to assess Velocity of
Detonation. However, they may ultimately require full scale (i.e., complete round) tests to assess
the IM properties of the munition following environmental exposure.
E.2.7.7 Electrical Components.
a. Where the munition contains electrical sub-assemblies (e.g., electronic safe/arm device,
weapon controller, seeker) these should be removed during BTCA for inspection and functional
checks. Functional checks should be performed initially on the initial sub-assembly, using the
factory test specification. Where this is not possible or does not allow full testing, then the sub-
assembly may require further disassembly to permit such testing.
b. Following this, full disassembly should be conducted for detailed component level
inspection. Specific points to observe are broken/loose joints (connectors and solder),
damaged/broken components, damaged/broken circuit board tracks, abraded/broken
cables/wiring, corrosion, dendritic growth (e.g., `tin whiskers'), condition of `potting' compound
(if present), and burst batteries.
c. Electrical resistance of igniters/EIDs (EEDs) should be checked, and EIDs (EEDs)
functioned using a normal firing pulse.
E-4
For Parts Inquires call Parts Hangar, Inc (727) 493-0744
© Copyright 2015 Integrated Publishing, Inc.
A Service Disabled Veteran Owned Small Business